How Basketball is Made: The Proven Secrets Unveiled

Basketballs are made through a process of shaping and molding rubber or synthetic materials. The process involves heating, molding, and shaping the materials into the desired size and shape.
The balls are then finished with the appropriate texture and design, before being quality tested and packaged for distribution. Basketball manufacturing is a meticulous process that involves several steps to ensure quality and optimal performance on the court. The materials used are carefully selected for durability and bounce.
The shaping and molding process requires precision to achieve the standard size and weight. Attention to detail in texture and design enhances grip and visibility. Quality testing is carried out to ensure the balls meet industry standards before being distributed for use in the game. We will delve into the detailed process of basketball manufacturing, exploring the materials used, the production steps, and the quality control measures employed in creating this essential sports equipment.
THE HISTORY OF BASKETBALL
Basketball was invented by Dr. James Naismith in 1891, using a soccer ball and peach baskets. The game evolved over time to include new rules and equipment, such as the creation of the modern basketball by Tony Hinkle in 1934, leading to the sport as we know it today.
The history of basketball is a fascinating journey that traces back to its invention and charts its evolution over time. Invention of the Game In 1891, Dr. James Naismith, a Canadian physical education instructor, invented basketball. Evolution of the Game Basketball quickly gained popularity globally and underwent significant rule changes over the years. With engaging simplicity and a versatile appeal, basketball’s history is a testament to its enduring allure.
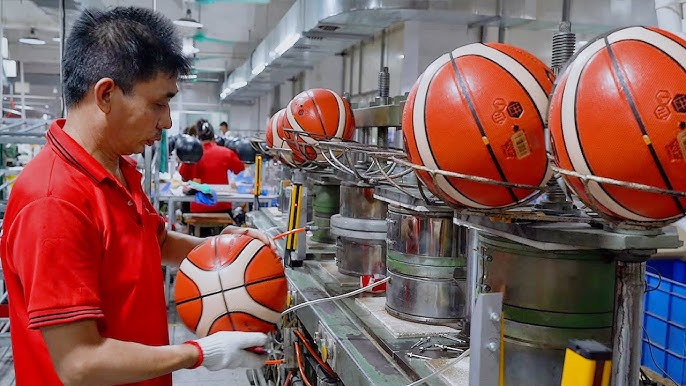
MATERIALS USED IN BASKETBALL PRODUCTION
When it comes to the production of basketballs, the materials used play a crucial role in determining the quality and performance of the final product. From the outer covering to the inner bladder, each material has specific properties that contribute to the overall construction of the basketball.
QUALITY OF LEATHER
The quality of leather used in basketball production directly impacts the durability and grip of the ball. The most commonly used leather is full-grain leather, known for its exceptional durability and natural grip. The grain pattern of the leather also influences the ball’s grip, making it easier for players to control during dribbling and shooting.
RUBBER FOR INNER BLADDER
The rubber used for the inner bladder of the basketball is essential for maintaining proper air retention and shape. High-grade natural rubber is often utilized to create the inner bladder, providing excellent bounce and responsiveness during gameplay. The quality of the rubber directly affects the overall feel and performance of the basketball on the court.
DESIGNING THE BASKETBALL
Basketballs are an essential component of the game, and their design plays a crucial role in the game’s playability and performance. The process of designing a basketball involves various intricate steps, with a focus on panel layout, logo, and text embossing. Each aspect of the basketball’s design is carefully considered to ensure optimal functionality and visual appeal.
PANEL LAYOUT
The layout of the panels on a basketball is a critical aspect that affects its aerodynamics and grip. The standard basketball is comprised of eight panels, which are traditionally made from synthetic leather or rubber. Each panel is strategically positioned to enhance the ball’s bounce and handling. The design of the panel layout is meticulously calculated to ensure consistency and balance in the ball’s flight trajectory.
LOGO AND TEXT EMBOSSING
Embossing the logo and text on a basketball is a distinctive branding element that adds visual appeal and recognition. The logo and text are typically embossed onto the surface of the ball using heat and pressure to ensure durability. This process requires precision to maintain the ball’s uniformity and texture while integrating the branding elements seamlessly.
PRODUCTION PROCESS
When making basketballs, several precise steps are involved in the production process.
CUTTING THE PANELS
The first step in producing basketballs is cutting the panels.
- Design templates are used to outline the panels onto the synthetic leather.
- The panels are cut with precision to ensure consistency in size and shape.
ASSEMBLY AND STITCHING
After cutting, the panels are assembled and stitched together to form the basketball.
- The panels are aligned and connected using strong thread and industrial stitching machines.
- Skilled workers ensure the seams are sturdy and durable for gameplay.
QUALITY CONTROL AND TESTING
Crafting basketball involves rigorous quality control and testing to ensure durability and performance standards are met. Each component undergoes meticulous checks before assembly and final evaluation, guaranteeing a reliable product for players worldwide.
In the process of manufacturing basketballs, quality control, and testing play a vital role in ensuring that each ball meets the stringent standards set by the industry. This ensures that players, both amateurs and professionals, enjoy a consistent and reliable playing experience. The quality control and testing process consists of various stages, including the air retention test and weight and size verification.
AIR RETENTION TEST
Determining the air retention capabilities of a basketball is crucial to its performance on the court. The air retention test involves inflating the ball to the specified pressure and then monitoring it over a period of time to check for any significant loss of air. This testing procedure aims to ensure that the basketball maintains its optimal bounce and firmness throughout a game. By conducting thorough air retention testing, manufacturers can identify any defects or issues with the ball’s construction.
WEIGHT AND SIZE VERIFICATION
To provide a fair and consistent playing experience, basketballs must adhere to strict weight and size guidelines. Manufacturers meticulously verify the weight and size of each ball during the production process. This involves measuring the circumference, diameter, and weight of the ball using precise instruments. The measurements are cross-checked against the standard specifications set by various basketball organizations. This meticulous verification ensures that the basketballs are uniform in size and weight, enabling players to develop their skills and perform to their best abilities.
In conclusion, quality control and testing are essential steps in the manufacturing of basketballs. Through the air retention test and weight and size verification, manufacturers ensure that each ball meets the required standards for optimal performance on the court. With these stringent quality control procedures in place, players can trust that their basketballs are of the highest quality, allowing them to focus on the game.
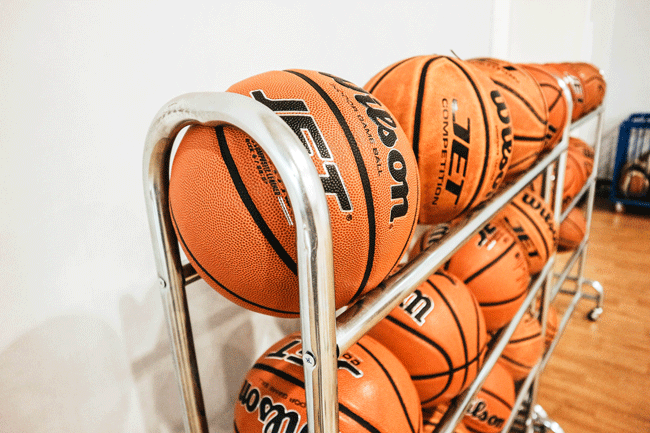
BRANDING AND PACKAGING
When it comes to marketing a product, branding, and packaging play a vital role. The same goes for the world of basketball. Not only does the quality of the basketball matter, but its brand identity and how it’s presented to the consumers are equally important. This blog post will explore how branding elements are applied to basketballs and delve into the packaging designed for distribution.
APPLYING BRANDING ELEMENTS
Branding elements are essential in creating a strong identity for a basketball product. These elements include the brand logo, colors, typography, and tagline slogans. For basketball manufacturers, applying these branding elements creates recognition and differentiation in a crowded market.
- Brand Logo: The brand logo serves as the visual representation of the basketball manufacturer. It is strategically placed on the basketball, usually near the center, to ensure maximum visibility during gameplay.
- Colors: Each basketball brand often has its unique color scheme, which helps consumers associate a particular color with a specific brand. For example, the iconic orange used in the Spalding basketballs instantly comes to mind.
- Typography: The choice of typography on the basketball can also contribute to its brand identity. Whether it’s bold and solid lettering for a more traditional feel or sleek and modern fonts for a contemporary look, typography plays a significant role in reflecting the brand’s personality.
- Tagline Slogans: Many basketball brands incorporate catchy tagline slogans that resonate with consumers. These short phrases not only communicate the brand’s values but also create an emotional connection with the target audience.
PACKAGING FOR DISTRIBUTION
Packaging for the distribution of basketballs is designed with two main goals in mind: protection and marketability. The packaging must ensure that the basketballs are well-protected during transportation and storage, while also catching the attention of potential buyers.
- Protection: Basketball packaging typically consists of durable materials like cardboard or plastic. Inner layers of padding are incorporated to safeguard the basketballs against impacts and potential damage.
- Marketability: In addition to protecting the basketballs, the packaging is designed to be visually appealing and informative. Eye-catching designs and vibrant colors are used to capture the consumers’ attention and entice them to choose a specific brand over others. Relevant product information, such as the brand story, features, and benefits, is also included on the packaging to persuade potential buyers.
In conclusion, branding and packaging are crucial factors in the success of a basketball product. By applying effective branding elements and creating visually appealing packaging, basketball manufacturers can establish a strong brand identity and attract consumers in a competitive market.
ENVIRONMENTAL IMPACT AND SUSTAINABILITY
Basketball production has a significant environmental impact. Understanding sustainability in this process plays a vital role in reducing the carbon footprint.
CHALLENGES IN RECYCLING
- No universal recycling system for basketball materials.
- Difficulty in separating different components for recycling.
EFFORTS FOR SUSTAINABLE PRACTICES
Companies are adopting sustainable measures like using recycled materials and eco-friendly production techniques.
Basketball manufacturers strive to reduce waste through responsible sourcing and efficient manufacturing practices.
THE FUTURE OF BASKETBALL MANUFACTURING
As technology continues to advance at a rapid pace, the future of basketball manufacturing is set to undergo groundbreaking changes. From innovative materials to automated processes, the potential for growth and improvement in basketball production is limitless. Let’s delve into the key aspects that will shape the future of basketball manufacturing.
TECHNOLOGICAL ADVANCEMENTS
Cutting-edge technologies are revolutionizing the way basketballs are manufactured. Robotics and automation are streamlining production processes, leading to increased efficiency and precision. Digital imaging and 3D modeling are being utilized to create highly customized designs and enhance performance characteristics. Additionally, smart manufacturing systems enable real-time monitoring and quality control, ensuring that every basketball meets the highest standards.
TRENDS IN MATERIAL INNOVATION
Material innovation is at the forefront of the future of basketball manufacturing. Nanotechnology is being harnessed to develop advanced composites that offer superior durability and performance. Bio-based materials are emerging as sustainable alternatives, reducing the environmental impact of basketball production. Furthermore, ongoing research into elastic polymers and energy-absorbing foams is paving the way for enhanced bounce and responsiveness in basketballs.
FREQUENTLY ASKED QUESTIONS ON (HOW BASKETBALL IS MADE)
HOW ARE BASKETBALLS MANUFACTURED?
Basketballs are made by fusing synthetic leather panels, applying engraving, adding rubber bladders, and performing quality checks.
WHAT MATERIALS ARE USED TO MAKE BASKETBALLS?
Basketballs are made using synthetic leather, nylon or polyester thread, rubber bladders, and adhesive materials.
HOW ARE BASKETBALL HOOPS PRODUCED?
Basketball hoops are manufactured by welding or assembling steel components, applying powder coat finishes, and ensuring durability.
HOW ARE BASKETBALL COURTS CONSTRUCTED?
Basketball courts are constructed by preparing the ground, leveling, applying layers of asphalt or concrete, and marking the court lines accurately.
CONCLUSION
As we’ve unraveled the process of making basketballs, it’s clear that craftsmanship and innovation collide in the creation of this iconic sports essential. From raw materials to skilled hands, every step contributes to crafting a high-quality product that fuels the love for basketball worldwide.
Dive deeper into the artistry behind the game.